The MSA from KRÜSS is inline-capable thanks to the available API and thus offers us the chance for Industry 4.0 quality control.
Ringo Köpge
Research Associate, Fraunhofer CSP
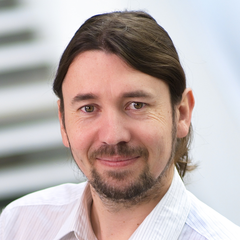
Solar energy is currently experiencing the greatest growth among renewable energy sources worldwide and has now overtaken wind power in terms of annual gigawatt capacity (as of 2019, source: www.bmwi.de). Facilities such as the Fraunhofer Center for Silicon Photovoltaics CSP are ensuring that the photoelectric effect is used ever more efficiently and thus more economically, further driving this positive development. As a research associate at the Fraunhofer CSP, Ringo Köpge is leading a project to optimize the manufacturing and quality assurance process for wafers, which also includes contact angle measurement for cleaning control.
Wafers made of silicon are the precursor of common solar panels. They go through several etching processes after the raw wafer is produced, which would be affected by surface contamination. Therefore, the final cleaning control of the wafers is an indispensable step of quality assurance. Ringo Köpge, project manager at Fraunhofer CSP, has set himself the task of optimizing this. For the method of cleanliness testing, the scientist decided to use wettability measurements by means of the contact angle method, because the material testing is contactless and non-destructive and does not leave any traces on the sensitive surface when pure water is used. Köpge aims to answer two important questions: How can a successful final cleaning inspection of wafers be carried out that covers as many samples as possible, and how does the contact angle data collected in the process correlate with the efficiency of the finished solar cells?
Within the scope of the project, a model process was to be set up which, after successful completion, could be considered for industrial scaling of wafering quality control. An inline-capable, fast-working measuring instrument was a mandatory prerequisite for this, due to the large sample volume and so that the measurement can be performed immediately after cleaning. Köpge decided in favor of the KRÜSS Mobile Surface Analyzer – MSA, an instrument which can be operated by hand, but which is also designed for use in a robotic system. An interface (API) of the software of the MSA allows remote start of the wettability measurements and automatic query of the results by other software.
The equipment of the Fraunhofer CSP makes it possible to map the entire wafering process chain, depending on the problem at hand. First, a silicon single crystal doped with foreign atoms, the so-called ingot, is grown. This silicon ingot is bonded to a sacrificial plate and both are cut into 180 to 250 µm thick square wafers using a multi-wire saw. The optimization of all these steps, including the development of an adhesive for the sacrificial plate, has already been part of oter research projects. Depending on the issue, project partners also participate in the steps: PVA TePla AG from Wettenberg (Hesse, Germany) in crystallization and the company PV Crystalox Solar Silicon GmbH from Erfurt (Thuringia, Germany) in wafering.
After a pre-cleaning step that dissolves the adhesive for the sacrificial plate, the wafers pass through a series of ultrasonic baths in an automatic cleaning system to free them from silicon dust and organic contaminants and finally again from the surfactants from the cleaning agents.
During the subsequent inline inspection and classification into A and B wafers, the thickness is recorded, the optical quality is checked using a camera, and finally the contact angle is measured, among other things.
The many process steps are accompanied by an equally large number of factors influencing the quality of the end product. However, the decisive current yield per area can only be examined on finished cells that are created from the tested wafers. At the heart of the investigation is the question of which process parameters and quality deficiencies have what effect and how strongly, and what the contact angle has on the expected output of the finished solar panel.
A huge amount of data is required to reliably determine correlations with the many independent influencing factors. As part of the project, thousands of differently processed and cleaned wafers therefore move through the inline quality control stations. For the evaluation and interpretation of the contact angle measurements, Köpge and his colleagues draw on methods of data science and cooperate with the company Kontron AIS from Dresden (Saxony, Germany). After successful completion of the project, the results promise to be groundbreaking for optimization and quality assurance in photovoltaic wafering.
The name Fraunhofer stands like no other for application-oriented research, which focuses on the development of innovative products and the close exchange with companies and universities. With 29,000 employees at more than 80 research institutes and countless partners and clients from industry, the Fraunhofer-Gesellschaft e. V. is the largest association of its kind in Europe.
The Fraunhofer Center for Silicon Photovoltaics CSP in Halle (Saxony-Anhalt, Germany) was spun off from the Institute for Microstructure of Materials and Systems IMWS as well as the Institute for Solar Energy Systems ISE in 2007. In addition to crystallization and wafering, the diverse research topics at the Fraunhofer CSP include analysis methods along the process chain, recycling of existing and development of new semiconductor materials, and data and process analytics.