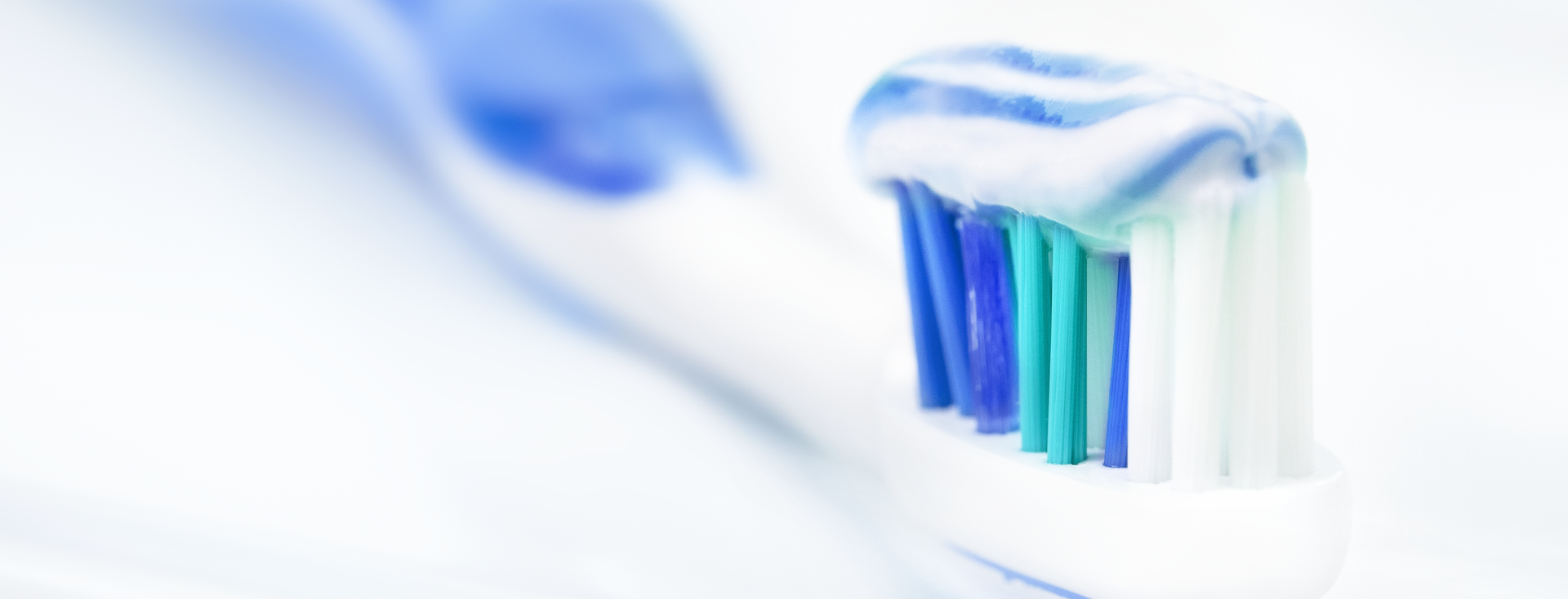
Foam behavior of toothpaste
Comparative analyses of the foamability and foam structure of dental care products
In addition to its medical and hygienic effects, toothpaste should also ensure a pleasant sensation in the mouth during cleaning. Foam formation plays a key role for both purposes: it is important for the distribution and cleansing effect of the toothpaste and is generally perceived as pleasant – provided not too much foam is formed. So optimizing the foamability and consistency of the foam formed is an important step in the development of toothpaste recipes. Whereby the number of expensive and time-consuming test group studies can be reduced if foam formation is tested in advance using suitable measuring methods. Equally important for quality assurance during production are meaningful analyses.
As part of an assessment of methods, we carried out a series of measurements on three toothpaste formulations using suitable measuring methods in order to compare their foaming behavior objectively. These involved reproducibly foaming diluted samples with a software-controlled stirrer in order to subsequently quantify their foamability and foam structures. The results enabled a clear identification of the differences between the various recipes.
Background
Virtually all toothpaste recipes include surfactants as foaming agents. The foam ensures the even distribution of polishing, enamel-strengthening and other active ingredients during cleaning. Fine-pored foam in particular ensures that even areas that are difficult to access are reached more easily. Moreover, the large inner surface created by the foam intensifies the cleansing effect.
However, excessive foam formation is mostly perceived as unpleasant. If, in addition, the foam is large-pored, i.e. has only a few bubbles per unit volume, then it does not have the desired degree of surface expansion, either. This makes foaming behavior a key quality characteristic of toothpaste.
A dental care product is subjected to expensive and time-consuming test group studies before it is launched or its recipe adapted. The number of tests required can be reduced in advance by foam analyses. In addition, foam measurements carried out with a reproducible method provide objective criteria for assessing a recipe that can be correlated with success in test group studies. If a recipe is optimized in such a way, routine foam analyses are also helpful within the scope of quality assurance.
Experimental part
Samples and their preparation
Three toothpaste formulations referred to as Sample A, Sample B, and Sample C were tested. Two of the samples contained sodium lauryl sulfate (sodium dodecyl sulfate, SDS) as a foaming agent and one type Cocamidopropyl betaine (CAPB).
Toothpaste | Foaming agent |
Sample A | SDS |
Sample B | SDS |
Sample C | CAPB |
Tab. 1: Toothpaste samples tested
Suspensions of 10 g/L were prepared from the samples. To do this 2.5 g of each of the samples were added to 60 mL of distilled water and stirred for 5 min. Next the suspensions were homogenized for 5 min using ultrasound and their volume filled up to 250 mL. The preparation of the solutions and the subsequent measurements were carried out at a temperature of 25 °C.
Measuring method and parameters
A Dynamic Foam Analyzer – DFA100 was used for measuring the foam height. Supplementary determination of the bubble structure was carried out with the Foam Structure Module – FSM.
With the DFA100, samples are reproducibly foamed. The upper and lower foam boundaries (liquid/foam and foam/gas) are captured during and after foaming by an LED bar and a line sensor bar positioned opposite to it.
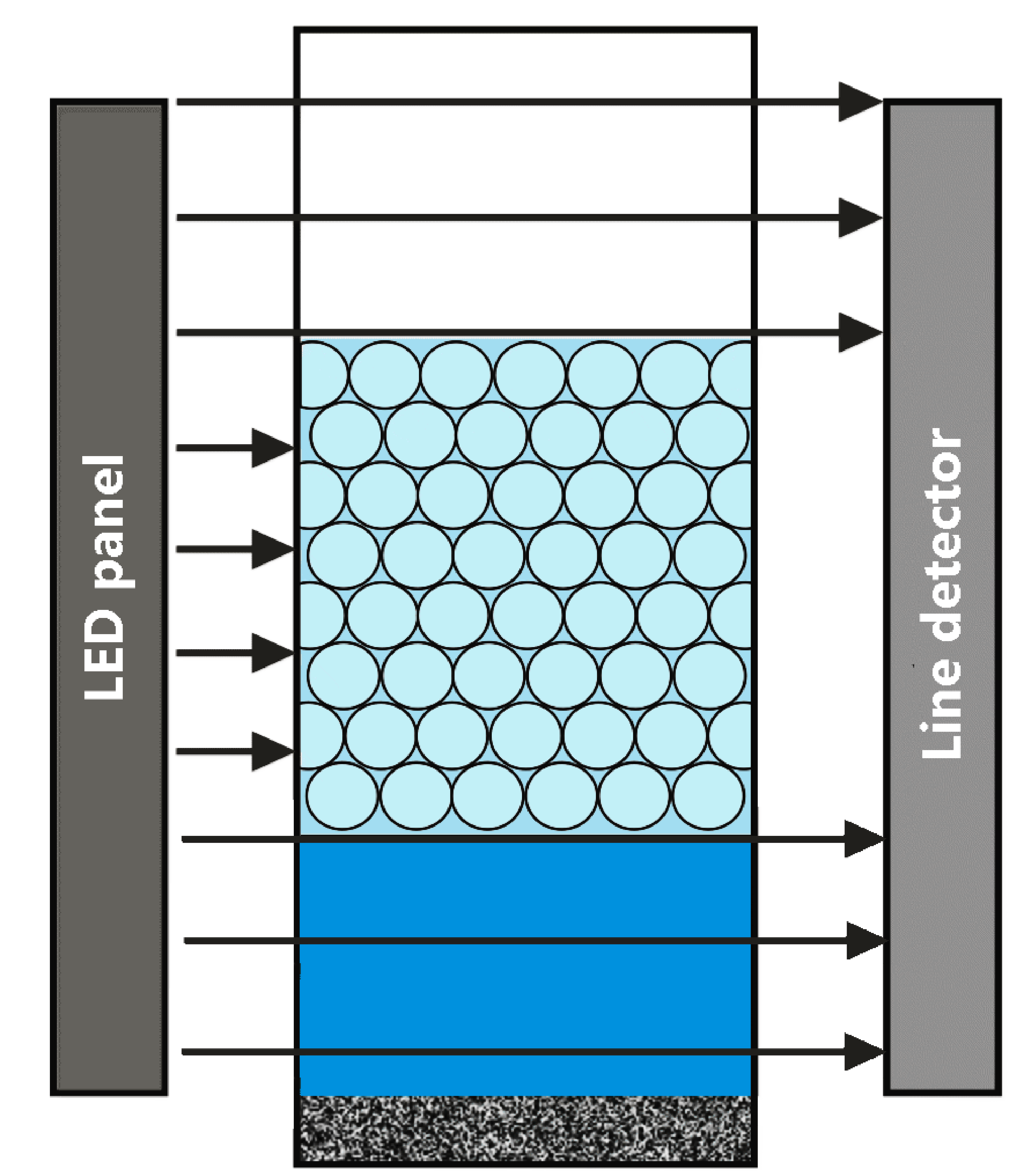
The measurement is depicted in a height curve that captures the formation of the foam in the foaming phase and its subsequent decay.
The Foam Structure Module – FSM enables parallel testing of the foam structure. It uses a special prism measuring column and captures all foam lamella on the glass sides with the aid of a video camera. The foam structure and its change over time with regard to bubble size and number are calculated by means of video image analysis.
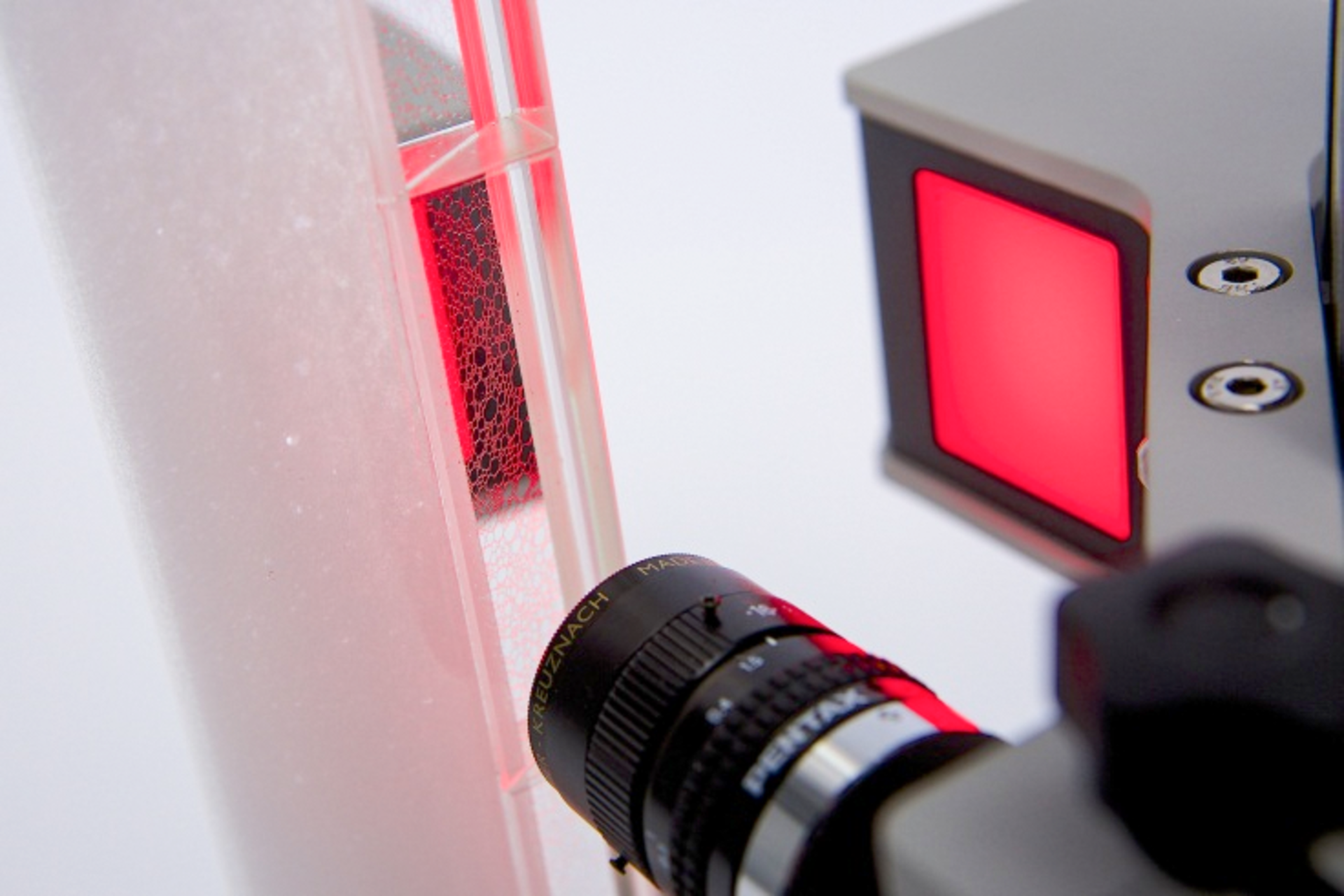
The DFA100 offers a choice of several foaming methods. A stirrer module with a two-winged stirring blade was used in these tests. Stirring comes closer to the way foaming takes place during cleaning of the teeth than, for example, sparging with gas.
A volume of 50 mL was used for each measurement, which was stirred at a speed of 4000 rpm for 40 s. The total measurement time was 900 s, so after 40 s of foaming the decay behavior was recorded for 860 s. Each sample was measured twice in order to test reproducibility.
Results
Foamability
The maximum height that occurs during measurement is a direct indication of the foamability of the sample. In the case of a stirrer module this is not measured at the peak of the curve, as this is created by the funnel-shaped turbulence during stirring. Instead the break point of the curve after the peak is decisive for the maximum total height.
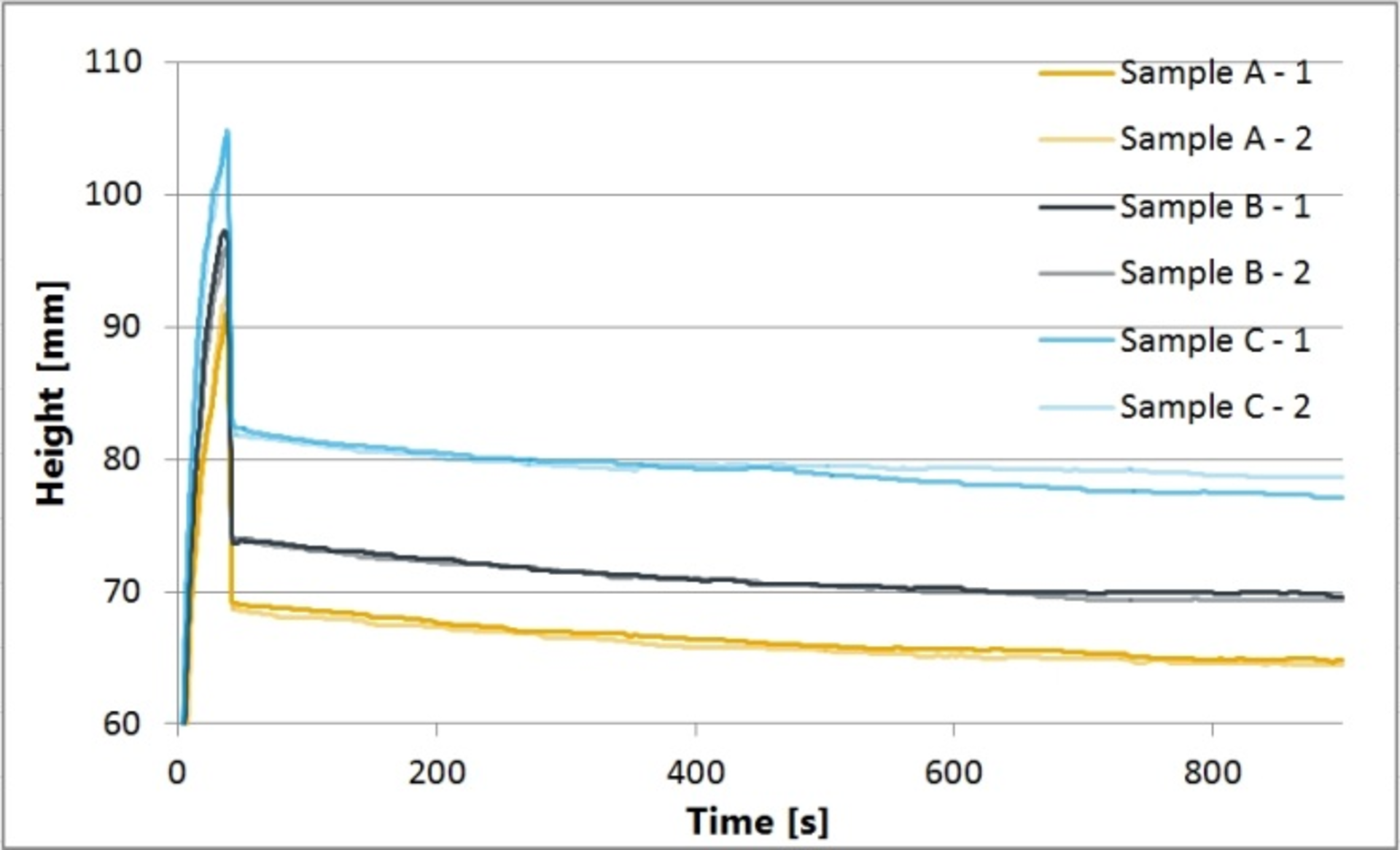
Foamability rises with significant differences in the sequence Sample A – Sample B – Sample C. This indicates that the sample with the CAPB surfactant foams the strongest. However, as the concentration of the form-forming surfactants in the toothpaste was not known, conclusions can only be drawn with regard to the intensity of the foam formed during cleaning, but not with regard to the efficacy of the foam-forming agents used.
Foam decay
All samples show the same flat rate of decay (see Fig. 3), in other words they all form relatively stable foams. This is beneficial with respect to dental care, because the foam formed does not decay immediately and can therefore be distributed more evenly. The significant differences between the samples with regard to the amount of foam remain constant over a long period of time. However, continuous reproduction of the foam during cleaning renders stability less important than foamability.
Number of bubbles
All three samples produce fine-pored foams with a correspondingly high number of bubbles; the differences shortly after foaming are marginal. In other words all foams produce the desired large inner surface.
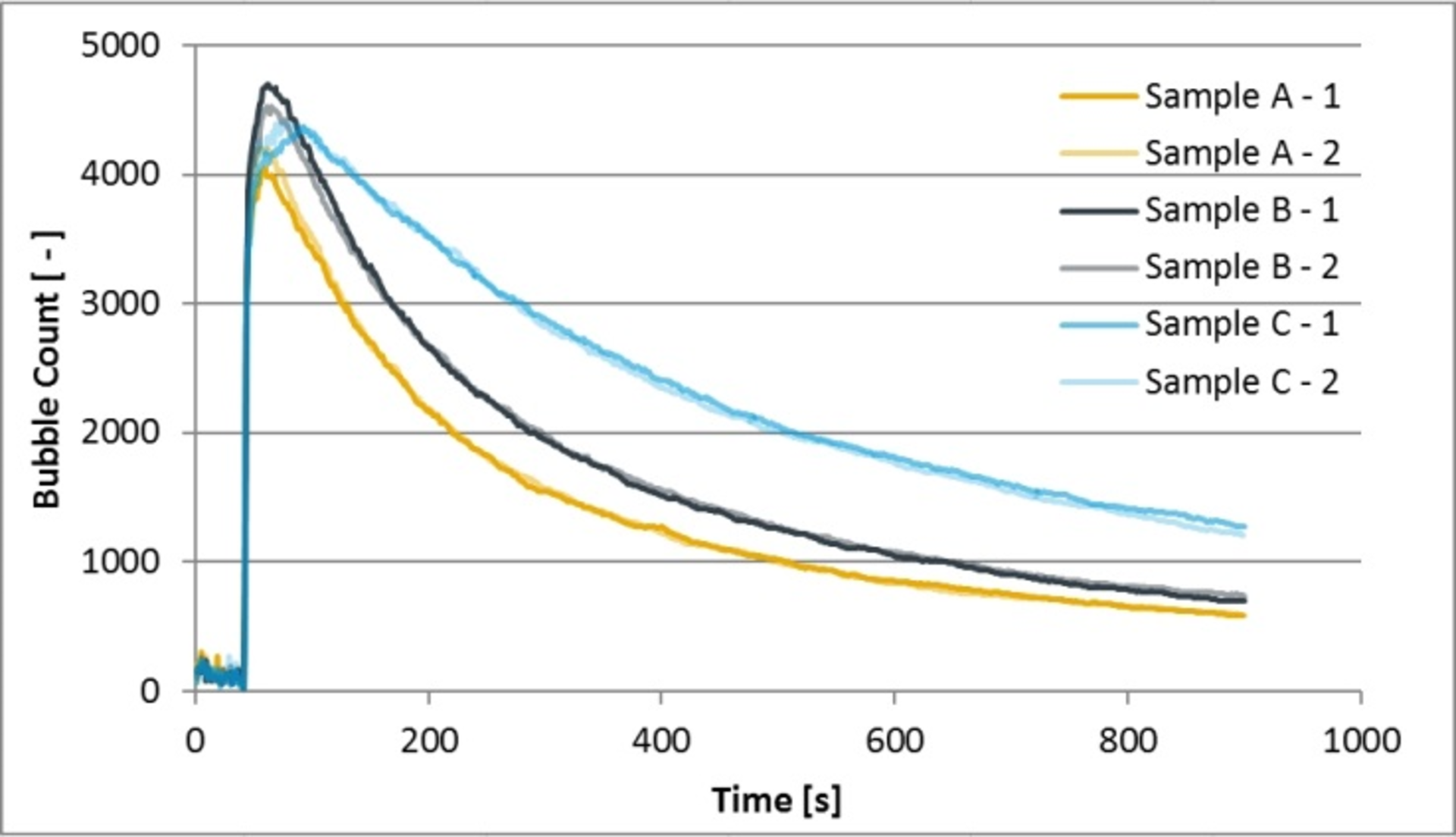
The subsequent decay of the foam goes hand-in-hand with a reduction in the number of bubbles and the simultaneous formation of larger bubbles. This process takes place at different speeds in the three samples, the fastest being Sample A, followed by Sample B and Sample C. The faster expansion of the bubbles in the case of Sample A and Sample B does not, however, constitute any great disadvantage, because foam is formed anew during cleaning. As is the case with the initial volume of foam, the initial foam structure is also more relevant than its development over time.
Reproducibility
The measured curves for the repeat analyses are very well superimposed, both in the case of foam height and foam structure measurements. This testifies to the good reproducibility of the foam measurements with the method presented.
Summary
Three toothpaste formulations were tested with the Dynamic Foam Analyzer – DFA100 and its Foam Structure Module – FSM. The tests focused on the volume of foam and the number of bubbles formed, as these two foam properties are of particular importance for dental care.
The good reproducibility of the results indicates that differences in the foaming behavior of the sample toothpastes can be shown clearly using this measuring method. According to the results, Sample C of the examined formulations with CAPB as its foaming agent (as opposed to SDS in the other two formulations) forms the largest volume of foam with small bubbles and a relatively long period of stability.
Such a test result does not at first allow any comparison of the quality of the samples, because the largest foam volume is not necessarily the criterion for assessing the optimum product. It can, however, be correlated with the test results of recipes that were judged to be successful by test persons. The measuring methods presented here can therefore be used in this way to provide objective parameters for the optimization of new products and to significantly reduce the number of test group studies that would normally be necessary. In addition such foam analyses are well suited for routine quality control during production.